Impulses
Today's business world is fast-moving. We offer you regular inspiration on current topics and developments. We share our insights and practical experience with you, give you a look behind the scenes of projects and present our ideas for the living spaces of tomorrow.
Article
Structures with a vision: How life cycle analysis' pave the way to sustainable buildings
Real estate
Sustainability
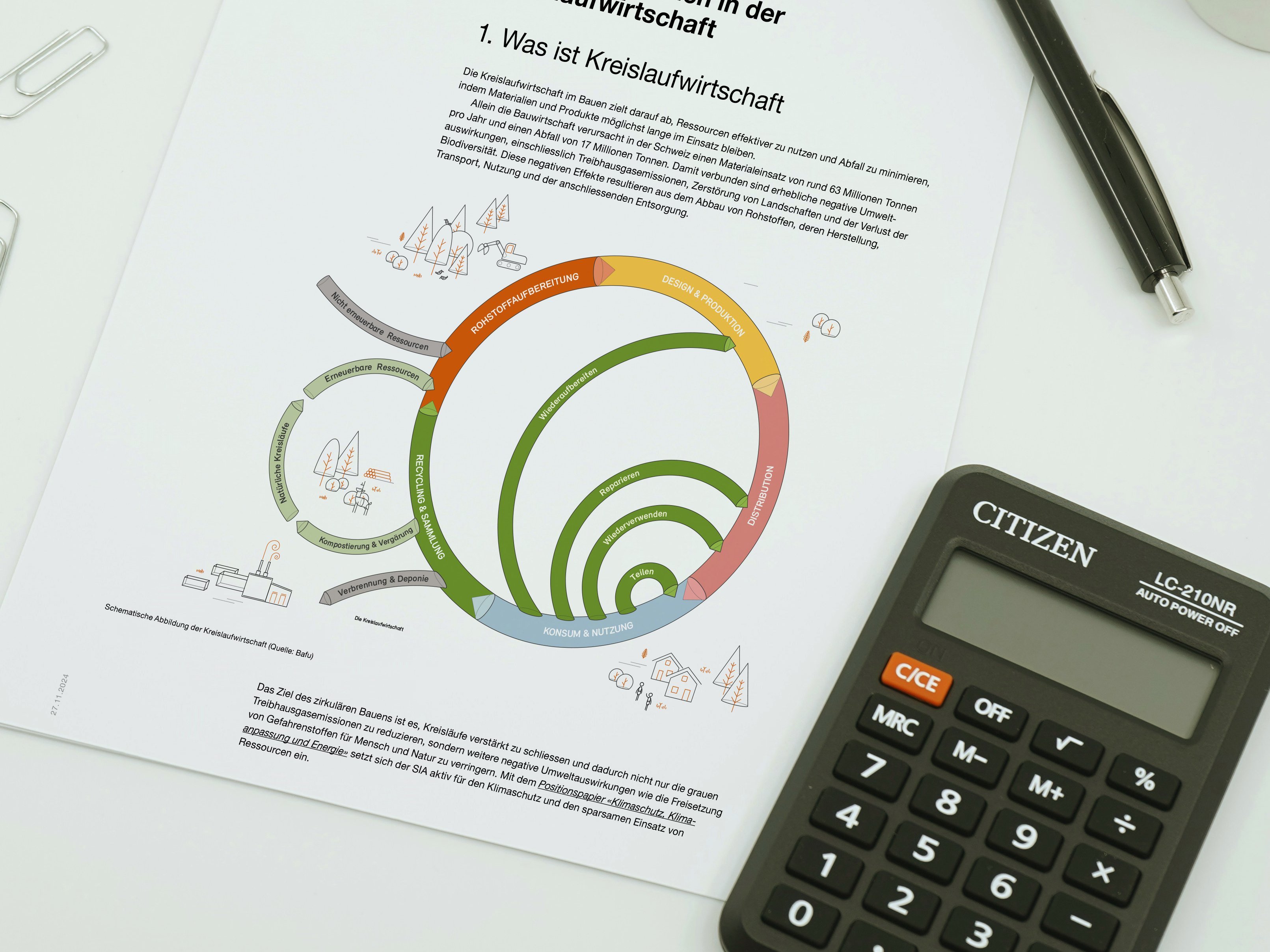
Impetus for sustainable living spaces
Your contact for media inquiries
We are happy to answer media inquiries and arrange interviews with experts in the field.